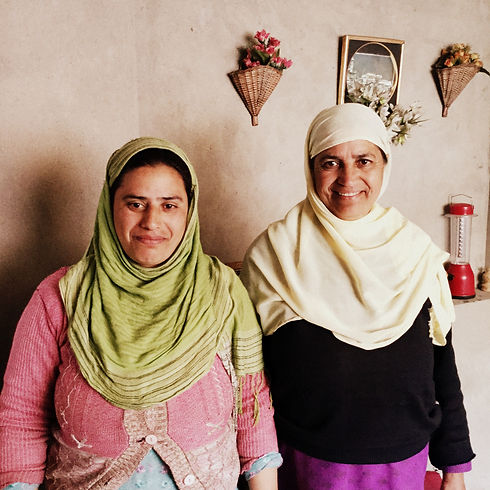
PASHMINA
our artisans & process
​
Srinagar, the capital of Indian-controlled Kashmir and once known as paradise on earth, is an ancient city nestled in a verdant valley. Under the shadows of the Himalayas, and built around the beautiful Dal Lake, it is home to a network of highly specialised master artisans. With each artisan focused on one task, together they create one of the most luxurious and softest textiles in the world: pashmina.
​
​
This community includes the men who card and clean the pashm fibre, the women who hand spin the yarn and the men who dye it, the families who prepare and load the looms, the men who hand weave the cloth, those who clip it of excess fibre and the others who's job is to hand wash it, and finally the men who embroider the finished cloth.
​
​

Dal lake. Source: Pallab Seth
Development issues are very different here in Kashmir compared to most of the rest of the country. Unlike many of their fellow weavers in India, in material terms Kashmiri weavers have it better off - they own their own, large brick or stone homes; they often own small patches of fertile land where they can grow their own food; they have access to plentiful water; the children are educated (Kashmir is second in India after Kerela in terms of school attendance) and child labour is almost non-existent.
The main challenge faced by Kashmiris is insecurity, which has been ongoing for decades. The conflict between the state and militants has ensured that there is no real job market in the region.
​
​
Security threats, regular curfews and lockdown of the city mean that home-based livelihoods are of particular relevance in Kashmir, and the hand-made pashmina industry supports thousands of artisans.
​
This community faces another danger - the rise of power-loom pashmina. While it is in fact illegal to machine spin and machine weave pashmina in Kashmir, this law is not enforced as demand for pashmina products outweighs what can be produced by hand. Even if the law were enforced, there are factories in nearby Punjab that produce machine-woven pashmina. So next time you buy a pashmina product, it's worth asking under what conditions it was woven - your choice of hand woven over machine woven is a vote of support for this skilled but fragile community.
​
​

The spinners
Shafika and her daughter Nazmai are native to Srinagar and have been spinning pashm fibres since childhood. Shafika’s mother taught her the skill, and likewise Shafika passed it down to Nazmai. Spinning is a task suited perfectly to the busy lives of Kashmiri women. It's like a side job that they can do in comfort at home, usually in front of the television, and around their household work schedules. Generally, Shafika and Nazmai will spend around 4 hours a day, a few days a week, spinning the valuable fibre on hand-run charkas (spinning wheels).
​
When asked if they enjoyed the work, Shafika shrugs. It’s a comfortable job in a city that has scarce livelihood opportunities, in particular for women, and she’s happy to earn the extra money. It allows her some independence, though much of the money is spent on the children.
​
​
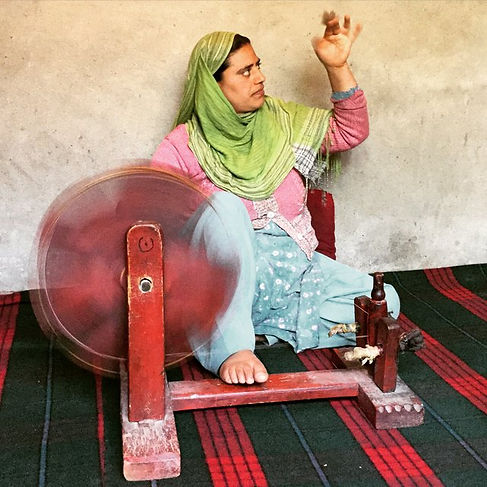
Payment is made directly to the spinners, who are always women, based on the final weight of the yarn they produce. They will receive Rs.250 (USD 3.50) for every 10g of pashm yarn which will take around 5 days of part-time work to spin. This amounts to around Rs.1000-1500 (USD 15-20) per month. It's not an independent livelihood, but in a society in which women do not generally do paid work, it's important for them.
Unlike weaving, which involves a whole host of different techniques and skills, spinning is just spinning, says Nazmai. There is no special technique to master - only speed and accuracy which comes with practice. Personally I beg to differ. Pashmina fibre is delicate and breaks easily. Having tried it myself, I think Shafika and Nazmai have enormous talent and patience.
​
​

The weavers
Zahoor (34 years, red shirt) and Bashir (36 years, white shirt) are brothers. Traditionally from an agricultural family, their father was a vegetable farmer in the outskirts of the city. Asked how and why they began weaving, they replied they were drawn to it when their father fell ill around 15 years ago. Many neighbours in their community were pashmina weavers and family friends taught them to use the loom.
The brothers have been weaving for 15 years. They weave all year round, for around 6 hours a day, depending on light and weather. In winter, the early evenings and sub-zero temperatures make it difficult to weave for so long. The pashmina looms are relatively small, and there are 3 set up in the upstairs room where they weave. A fourth loom is elsewhere in the house.
​
​
The whole family is engaged in one way or another in the pashmina business. While it is the men who traditionally weave pashmina - as across most of India, the women of the house have the laborious task of spinning the fibre into thread, and drafting the thread (loading the thread through the fine comb that holds the warp threads). The younger boys will prepare the thread for the loom.
​
While looms in India typically hold thread for 60m of fabric or more, the small looms of Kashmir typically hold thread for the production of around 12m of pashmina fabric. This is because the fibre is so much more valuable than the cottons and silks woven elsewhere in the country. Production is made on a much smaller scale here. It takes 10-15 days to complete the 12 meters of fabric. The full process - from loom loading to washing and drying takes a much longer 1 month.
​
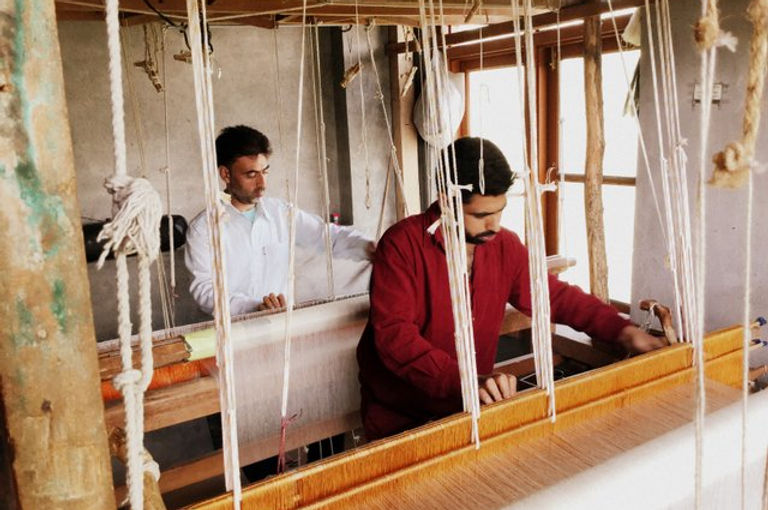
The brothers enjoy weaving; they earn their livelihood from this work, making around 8-10,000 INR (approx. USD 150) each a month. Additionally, they supplement their diet and income with some farming. Bashir has two young children. While he enjoys his work, he says he won’t teach the children to weave.
​
​
Work is getting more difficult as they compete with power-loom fabrics and the salary to be earned from weaving is still low compared to many other types of jobs. While Bashir will receive around Rs.1000 (USD 15) for a handloom shawl, that same size shawl in machine woven pashmina will sell for Rs.150 (USD 2.20).
​
​